Air Force Improvises With 3D Printing to Overcome Supply Chain Challenge
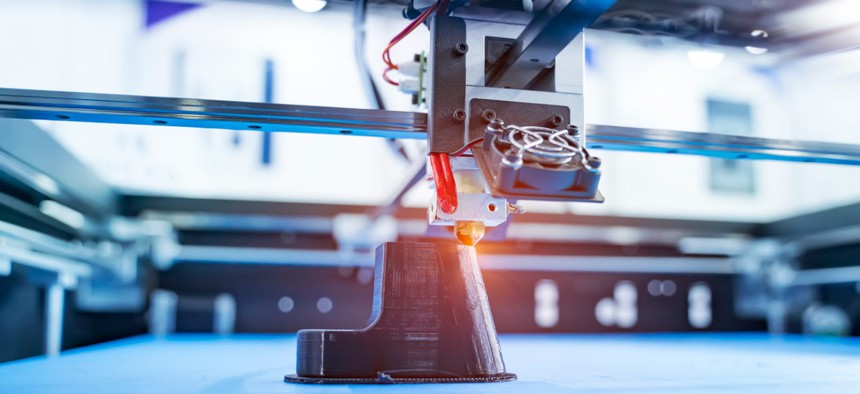
kynny/istockphoto
A senior airman’s creative idea resulted in money saved and capabilities improved at Joint Base Langley-Eustis.
Air Force officials in Virginia recently 3D printed a piece in a few hours that was needed to bring crucial refueling equipment back in service after almost a year of stagnation.
“The issue with the part and its availability was a supply chain issue,” Staff Sgt. Gabriel Macdonald told Nextgov on Friday.
Officials generally order new military vehicle and device parts for use before those in use break or need to be replaced. Modern constraints on the U.S. and global supply chains intensified by the coronavirus pandemic, however, meant necessary components weren’t so readily available over the last couple of years.
During a recent staff meeting at Joint Base Langley-Eustis, 633rd Logistics Readiness Squadron Fuels Training Supervisor Senior Airman Houston Sasser heard colleagues question Air Force leadership about a supply chain obstacle that was causing long-going inactivity for the high-lift, a vertical-extension platform for refueling operations.
One of the high-lift’s safety features is the flame arrestor, which is designed to prevent fire hazards involving combustible fuel-air mixtures. The flame arrestor cap failed—but replacements weren’t an option.
Hearing personnel’s concerns, Sasser suggested using 3D printing to create an inexpensive and more reinforced flame arrestor cap.
Via the advanced manufacturing process, operators can develop geometrically accurate, custom pieces often at a pace that’s much quicker than what traditional vendors can provide.
This advanced production option is being explored and applied by multiple military entities. For instance, the Naval Surface Warfare Center issued contracts to select vendors this month that involve pursuing novel prototype projects with 3D printing. Beyond Defense Department components, federal agencies have also turned to the emerging technology for health-related and other purposes.
With support from logistics readiness leadership, Sasser ultimately designed and produced the needed part in roughly 5 hours.
“By 3D printing the replacement flame arrestor cap, I was able to bring the high-lift back into service after nine months of inactivity and show the simplicity and ability to create complex parts or prototypes in theoretical solutions,” Sasser said.
It costs the Air Force only about 25 cents to produce the replacement pieces with added structural reinforcement.
“The unique part about the flame arrestor cap is that the pantograph systems that we use for Hot-Pit refueling require the same part,” Sasser noted. “In the event that there is an issue with a pantograph cap, we now have the means to quickly return them to service to enable 1st Fighter Wing operations.”
The senior airman was personally coined for the concept and solution.
Macdonald and 633rd Air Base Wing Public Affairs Chief of Media Operations Mike Reeves did not confirm the number of 3D printers functioning on the base, or plans for future applications.
“We're incredibly proud of the efforts of service members like SrA Sasser. Innovations like 3D printing enable our team at JBLE to continue to exceed Air Force Chief of Staff, Gen. Charles Q. Brown's, goals to accelerate change or lose,” Reeves told Nextgov on Monday. “We're excited to see more projects as our soldiers and [airmen and women] continue to be multi-capable innovators and problem solvers.”
NEXT STORY: Who’s in Charge of US Space Policy?